Porosity in Welding: Identifying Common Issues and Implementing Best Practices for Avoidance
Porosity in welding is a pervasive issue that frequently goes undetected till it causes considerable problems with the integrity of welds. In this conversation, we will check out the crucial aspects adding to porosity formation, examine its damaging impacts on weld efficiency, and review the ideal methods that can be adopted to decrease porosity occurrence in welding processes.
Typical Root Causes Of Porosity
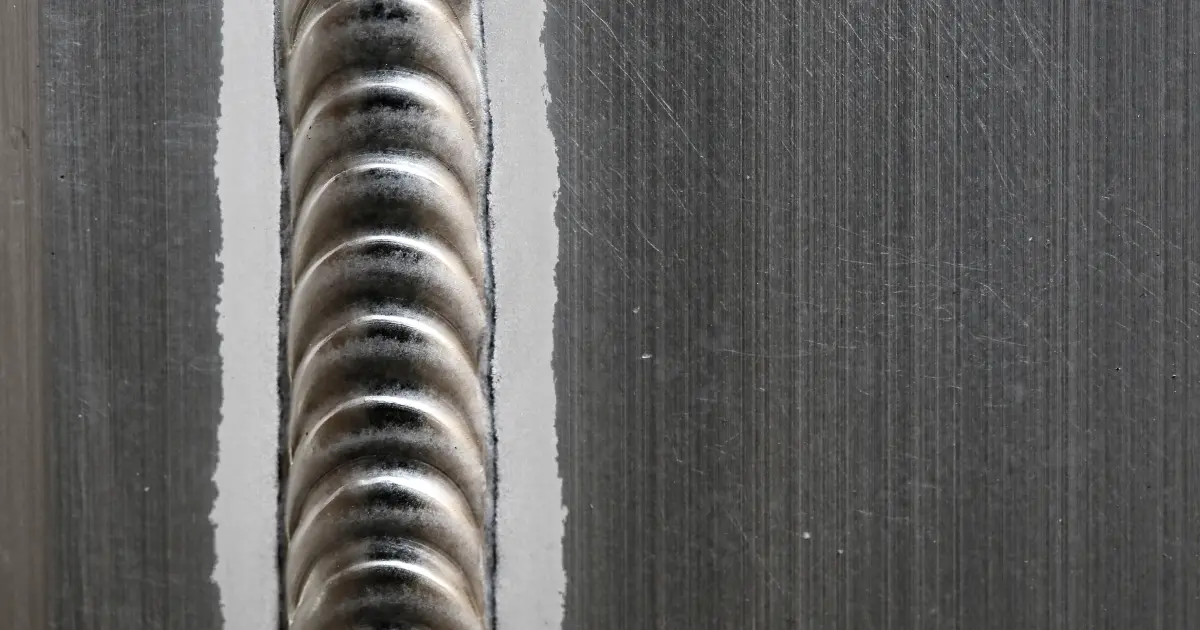
Another frequent culprit behind porosity is the visibility of impurities externally of the base steel, such as oil, oil, or corrosion. When these impurities are not effectively removed before welding, they can vaporize and end up being caught in the weld, creating issues. Furthermore, using unclean or wet filler products can introduce contaminations right into the weld, adding to porosity problems. To mitigate these typical root causes of porosity, thorough cleaning of base steels, appropriate protecting gas choice, and adherence to optimal welding specifications are necessary methods in accomplishing high-quality, porosity-free welds.
Impact of Porosity on Weld Top Quality

The existence of porosity in welding can substantially jeopardize the structural honesty and mechanical properties of welded joints. Porosity creates gaps within the weld metal, weakening its total toughness and load-bearing capacity. These gaps work as stress and anxiety focus factors, making the weld extra prone to cracking and failure under used lots. Additionally, porosity can minimize the weld's resistance to deterioration and other ecological variables, additionally diminishing its longevity and efficiency.
Welds with high porosity degrees have a tendency to exhibit reduced influence stamina and minimized capacity to flaw plastically before fracturing. Porosity can hamper the weld's capability to efficiently transmit forces, leading to premature weld failing and prospective safety hazards in crucial frameworks.
Ideal Practices for Porosity Avoidance
To boost the architectural stability and high quality of welded joints, what certain actions can be executed to lessen the occurrence of porosity during the welding process? Utilizing the correct welding method for the details material being bonded, such as adjusting the welding angle and weapon position, can additionally prevent porosity. Normal assessment of welds and prompt removal of any problems identified during the welding procedure are essential methods to prevent porosity and produce top notch welds.
Value of Correct Welding Techniques
Executing proper welding methods is extremely important in ensuring the architectural integrity and top quality of welded joints, developing upon the foundation of effective porosity avoidance steps. Welding techniques directly impact the total stamina and durability of the welded framework. One crucial aspect of proper welding methods is preserving the right warmth input. Extreme warm can bring about increased porosity as a result of the entrapment of gases in the weld swimming pool. Conversely, insufficient warmth might result in insufficient combination, creating potential powerlessness in the joint. In i loved this addition, making use of the ideal welding specifications, such as voltage, present, and take a trip speed, is essential for attaining sound welds with very little porosity.
Moreover, the choice of welding procedure, whether it be MIG, TIG, or stick welding, ought to line up with the details demands of the project to make certain ideal outcomes. Correct cleaning and preparation of the base metal, as well as selecting the right filler product, are additionally vital elements of proficient welding methods. By sticking to these best practices, welders can decrease the threat of porosity development and generate top notch, structurally audio welds.
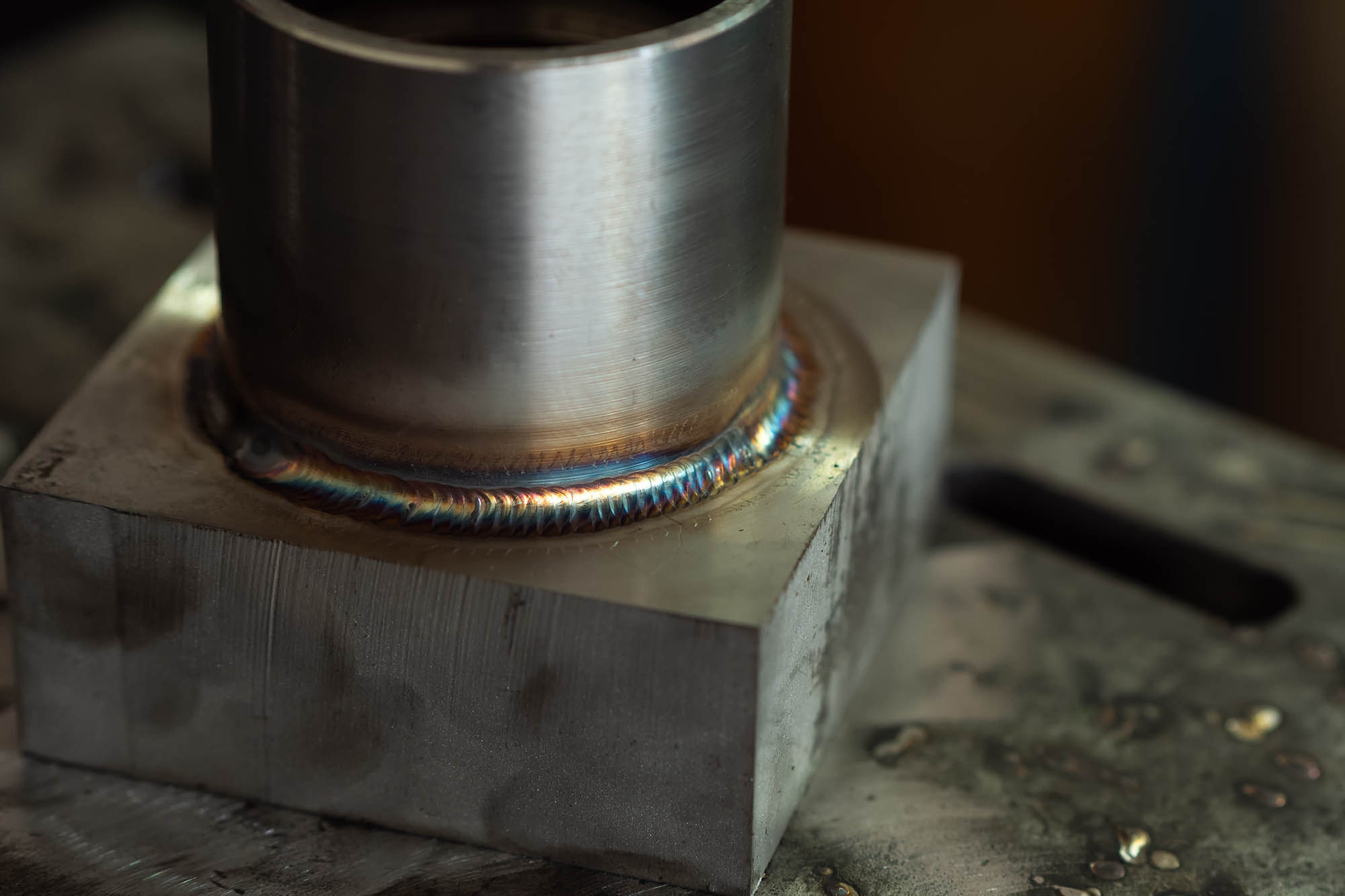
Evaluating and Quality Control Steps
Examining treatments are important to identify and protect against porosity in welding, making sure the stamina and toughness of the last item. Non-destructive screening approaches such as ultrasonic screening, radiographic testing, and visual evaluation are frequently utilized to determine prospective flaws like porosity.
Conducting pre-weld and post-weld assessments is additionally important in preserving quality assurance criteria. Pre-weld examinations try these out include verifying the products, equipment setups, and cleanliness of the job location to stop contamination. Post-weld examinations, on the other hand, examine the final weld for any issues, consisting of porosity, and confirm that it satisfies specified criteria. Implementing a detailed quality assurance plan that includes comprehensive screening procedures and examinations is extremely important to minimizing porosity problems and making certain the general top quality of welded joints.
Verdict
Finally, porosity in welding can be a common concern that impacts the quality of welds. By recognizing the common sources of porosity and executing best practices for prevention, such as appropriate welding strategies and screening steps, welders can make sure high top quality and reliable welds. It is vital to prioritize avoidance site link techniques to reduce the occurrence of porosity and maintain the integrity of welded structures.